Installations | Repairs
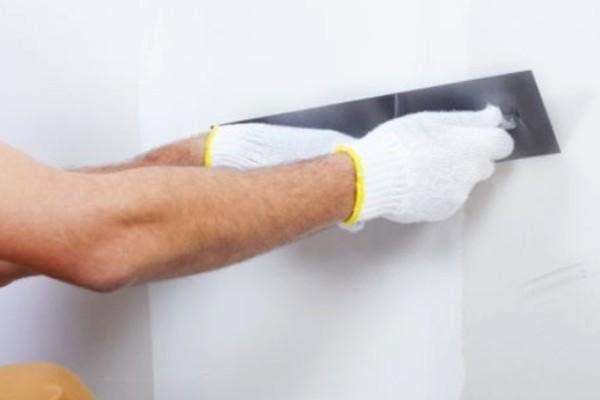
We can install or repair everything from your old foundation, new floorings, new tiles in your shower to the shingles on your roof. We will help you decide what the best thing for you and your home is; by working closely with our clients we ensure their installations are perfect and exactly what they want every time. At Ottawa Renovation & Construction we always provide all possible options for you to choose the best option together with us.
Drywall/Mudding/Fire-Taping
DRYWALL BASICS FOR THE FINISH YOU WANT
It’s been referred to as many different things—sheetrock, gypsum board, wallboard, and, of course, drywall. However, all these terms refer to the same thing: a panel consisting of a gypsum core surrounded by paper backings. It’s become the most popular form of wall surfacing, quickly replacing the plaster found in older homes. Why? Because it’s cheaper, lighter, and easier to install. Plus, it’s not as hard as plaster, so it won’t crack as fast, but it’s also stronger: it tends to hold objects (such as picture frames) without special hanging devices. Though it’s everywhere you look, this material may still be a mystery to homeowners. Therefore, here are some basics from the very start to its final finish.
HOW DO YOU CHOOSE AN APPROPRIATE PANEL?
Sheetrock comes in 8-10′ panels that are typically a 1/2″ in width, though it may be a bit thicker (5/8″) for ceilings, garages, or basements. Since it’s constructed of paper, it can be vulnerable to moisture damage, so for wet areas of the house you may want to invest in green board: it’s water-resistant and can withstand high levels of humidity.
SKELETAL STRUCTURE: WOOD OR METAL STUDS?
Once the panels are selected it’s now time to hang them up. But what do they hang on? In other words, where to do walls come from? Before installing gypsum board, a wall frame must be erected. Though it’s eventually covered up with sheetrock, framing is the most important step in the process, so the materials you select are just as critical.
Wood Studs: Wood is the more popular framing material since it’s sturdier and less expensive. Plus, it doesn’t transfer energy and therefore creates a better insulator than steel products. But the main reason it’s used so often is due to its easy installation: most contractors are used to working with lumber and therefore it is the preferred method.
Metal Studs: However, steel materials come with their own benefits when compared to wood. Steel won’t age, warp, rot, or deteriorate. It’s impenetrable against termites, ants, and other pests. It’s fire-proof and flexible, which means it won’t fall apart during earthquakes. Also, during installation, it’s light and forgiving: since it’s simply screwed together, if a mistake is made it’s easily corrected without wasting materials. Plus, it’s environmentally friendly when it comes to saving our natural resources.
Final Finishes: Textured Drywall or Smooth Drywall?
Once the panels are nailed or screwed to the framing, the wall is complete. However, you don’t want to be stuck with an ugly gray façade. So it’s time to finish things up. The joints between the panels will be covered with tape or compound. Also, you’ll have to prepare the surface for decoration. Depending on whether you want wallpaper, paint, or special faux finishes, you must create either textured drywall or smooth drywall.Textured Drywall: Textured drywall ranges from light to heavy, with both simple and complex grains. A sprayed texture is the most popular application method since it uses less labor and isn’t as costly as hand-applied finishes. Fine to coarse grades of texture can be sprayed and left in place or quickly flattened with a hand trowel (“knock down” style). But textured drywall can be made coarser by adding granules (of foam, for instance) to the compound or paint.
Smooth Drywall: There are two types of flat wall finish: for wallpaper (a layer of joint compound is applied and sanded) and for paint (which leaves a slight pebble finish). Many faux painting effects require a smoother finish as well.
Unfinished Sheetrock: Most people elect to keep their walls unfinished in garages or other work areas since the look isn’t as important and it saves on expenses.If you are matching existing drywall and having it professionally installed, it’s important to let your service professional know the size and surface type so a more accurate estimate can be delivered. Most contractors bid on the installation by the area, and they often charge more for any specialty finishes. So always be aware of all options available to you and ask for finish samples to avoid accidental surprises with the complete project.
Retaining Walls with Concrete, Block or Wood
Retaining walls were first used for the simple and necessary task of holding back earth. Erosion is a natural process, but when it means soil being washed off your property or worse, accumulating against the side of your home, a retaining wall can be an essential protectant part of your landscaping. These walls are not only functional, though. A garden wall is a retaining wall meant for purely aesthetic uses, allowing a hill to be made to enclose a garden. Any of these walls can offer more usable surface area in a landscape design and are a terrific component to your home.
RETAINING WALL MATERIALS
Traditionally these walls were made from railroad ties and found stone. The land is dug back, the stones or wood placed as a wall, and land filled back in behind, creating two flat surfaces where there once was a hill. The process is no different today but the uses and materials have changed. While railroad ties, and now treated landscape timber, are still used, whenever you put wood directly against soil there is a great potential for rot if improperly installed or treated. Stone is still used, of course, and offers a defence of rot and much more of a natural look—a classic look when installed properly by a stonemason. Brick can offer a more staid look, while concrete blocks are inexpensive and simple. Other options include masonry, poured concrete, and steel, but the choice of material has everything to do with what you plan to do in front of the wall.
USE OF THE LAND
Retaining walls are most often still used to simply keep back or move earth. This often means leaving the land as cut grass, offering more usable yard for the property. This decision leaves the walls exposed, though, which places a lot of importance on the look of those walls. A cheap masonry job will become an eyesore, a concrete flat wall will look commercial or industrial, while a quarried stone retaining wall will become something you want to show off. The purposes of these walls vary. If it is to retain earth or create more yard space, you will want to match the design to your home’s exterior design. And if it is to create a layered landscaped look, then it is less about the walls and more about the landscaping design put in after the installation.
GARDEN WALLS
A garden wall is a type of retaining wall that encloses a garden. Also called a screen wall, it is often used as a device to create a tiered or terraced garden. A garden wall is not a structure that is designed to hold the weight of soil. This can be an elegant addition to any home design, creating a wall of flowers and shrubbery where there was once just a hill of hard-to-mow, hard-to-grow grass. Next to a pool, walkway or patio it might brighten your summer days. For a home’s garden window, it can even make a tremendous difference in the everyday feel of your home.When looking into the type of retaining wall you want for your homes frontyard or backyard be sure to also consider environmental concerns. Railroad ties and treated timber have fallen out of favor due to the chemicals used, while flat concrete walls do not allow proper drainage. More common now because of its mix of look, cost, and environment-friendliness, is the segmental retaining wall, or retaining wall blocks. These concrete slabs are pre-made to create a specific design feel while also allowing for drainage. Whatever materials you choose, a retaining wall will offer you more use of your land with the added benefit of creating a unique and elegant look to your landscape design.
Excavate or Grade the Slope of the Grounds
FIXER-UPPER: HOW TO GET STARTED
Every family and newly wed today is trying to make extra money planning for kids.
Now that you have bought your fixer-upper and can see the possibilities, it’s still difficult to know exactly where to start. Depending on the size of the home, if you are already living there, and your frequency of visitors, there are many options to consider as the best place to start.
NON-OCCUPIED FIXER-UPPER
If you still have somewhere to live or are just fixing this home as an investment, you have more money saving options because you can buy in bulk rather than room by room. If you are just now in the market for a fixer upper, click this link to read more about purchasing fixer uppers.
Walls: The first thing you should do is rip out the drywall, or the lathe & plaster if the home is pretty old. If you know for certain that the wiring is solid and the walls are fine, don’t worry with this. Tearing out the walls is called “gutting”, and once your home is gutted, you can start your remodeling from the ground up.
Wiring and Insulation: Upgrade or replace the wiring. This is a good place to add more load so that you can have more appliances than the house was originally wired for. Next, insulate as heavily as you can and don’t forget to insulate around the windows.
Floors: If the floors are in poor shape or you just want to go with a different material, now is the best and easiest time for this.
Windows: Since you have the walls out, windows are a good money saver if the current windows are old or in bad shape. Plus there are many different grades of windows that can fit any budget.
The remainder of the home, since no one is in it, can be done in whatever order you choose since it won’t upset anyone’s life.
OCCUPIED FIXER-UPPER
There are a few schools of thought about remodeling when you are living in your fixer-upper.The broad plan is to begin tearing up everything: ripping up floors, pulling out bad trim, choosing paint colors. People who like this method usually work quickly and like to spend every waking minute working on their home. If it doesn’t bother you to have materials strewn about, and portions of every room in some degree of disrepair, then start working.
However, if you like to go slowly and maintain some degree of order, then there is another plan.If the bedrooms need work, choose the one you want to be yours, most likely the master, and remodel it to where there is nothing more to be done to it. Reason being, after you are finished with your bedroom you can retire every night in comfort no matter how torn up the kitchen or bathroom or living room is.
From here, continue to remodel only one room at a time. No matter how tempting it is to start ripping down trim, wallpaper or stripping paint, you have to resist. It is much easier to close off one room than to apologize to guests for multiple rooms being in disarray.
At some point, no matter how handy you and your spouse are during your Reno you will need some professional help. Don’t think that you are losing value by doing this. Matter of fact, don’t think that you are losing value by contracting all of it. This is nothing to be ashamed about. Having a fixer-upper means you are getting valuable property at a lower price because it is not in optimal condition. No matter who physically does the work, the home will be exactly how you want it to be, not to mention that it will be in better shape. If you happen to be to a point in remodeling your fixer-upper where you need some help, click this link and select from any of our categories for which you need help, and get matched to one of our prescreened remodeling professionals.
The kitchen and bathrooms are difficult because when you begin to tear them up, you limit your capacity to live normally. However, these are the areas in a home that have the greatest return on investment, and the first place people look when buying your home.
Some people like to paint first, which is a fine strategy, since this is the same process as many home builders. However, during the process of remodeling, walls get bumped and gouged and scraped so it also makes since to save this until the end.
With kitchens, plan ahead for the day your sink will be out of commission. Don’t tear it out on Friday when the installer isn’t coming until Monday. Always be thinking about minimizing the time that any part of your kitchen will be non-working.
If there is only one bathroom, you better have a strong marriage. Bathrooms are tricky, so just like kitchen sinks, be ready to finish the job once you start.
FIXER-UPPER FINISH
The two camps basically come down to how many visitors you will have. If you will have many and don’t want them to see your home torn up in nearly every room, definitely doing one room at a time makes sense for both the entertaining house and the busy house. However, if you are good at finishing things quickly and you’d rather have the whole house painted than one room at a time, then this is probably the better choice.
Foundation Installation or Repair
Stamped concrete is increasingly the material of choice for many home design projects today. Stamped concrete patios are designed to look like flagstone, Spanish tile, or quarry stone. Other stamped concrete patterns are used as kitchen counters, beautiful ceramic tile facades on the wall, and a fireplace hearth. This technique is not new, and has been so well refined, that you’ve likely walked past it, or over it, and assumed it was real quarry stone or fired tile.
THE NEW AND REFINED USES OF AN OLD FAVORITE
Don’t think of the old bland gray concrete—that efficient, sturdy material people use when they want something that is strong, lasts long, is inexpensive and is easy to work with. Or, think about concrete in the hands of an artist. The most basic concrete is small bits of stone bonded together. When these bits are at their smallest, and various pigments and lacquers are applied, stamped concrete can become slate, ceramic tile, cobblestone, marble, and more. The options are endless. When using stamped concrete it is also possible to mix patterns and colors, introduce edges, designs, centerpieces, and band work. The design is only by limited your imagination.
PATTERN STAMPED CONCRETE, STENCILED CONCRETE, AND ACID STAINED CONCRETE
The most common type of stamped concrete is pattern-stamped. This basically involves “stamping” patterns into freshly placed concrete and applying color, as well as any weather-treatment, stain or lacquer needed. Stenciled concrete is similar in that a stamp is used, only rather than a full-sized “stamp,” a stenciled sheet is used. This process is less expensive but also less reliable. While color is often applied to the top of the concrete after it is set and stamped, another process, acid staining, is an interesting one to consider.
ACID STAINS
Acid stained concrete is a simple staining process that can be used even when you are not using stamped concrete. Acid stained concrete mixes chemicals into the concrete which causes a reaction with minerals that are already present to create various colors. Because the color is then mixed in according to the mineral deposits in the concrete, it creates a mottled look that is almost identical to natural marble. These colors are natural colors, earth tones like the browns, reds and greens you see in classic architecture. This coloration can create a beautiful, natural look to any driveway, walkway, entranceway, or even your kitchen or bathroom floor.
Stamped concrete offers terrific options in interior design. You’ll often find concrete countertops that look as beautiful as any ceramic tile or granite countertop around. But like any other trade that requires some artistry, it is important to find the right company for the job.
With our company service, and a bit of imagination, stamped concrete will offer you an unlimited number of colors, textures and designs to work from.
Brick or Stone Siding Facts
CONCRETE FOUNDATIONS
While concrete foundations are one of the very best kinds of foundations out there today, its stability relies on proper site preparation. Soil and slope are the two biggest factors to ensure you get a solid, long-lasting foundation, but other climate conditions, weight bearing, and basements can also be important considerations for your concrete foundation.
Concrete Foundations and Property Slopes
Your contractor needs to know the existing slope of your yard so he can prepare the site for the foundation. The contractor will design your foundation so water drains slope away from your house, keeping the foundation dry. He may need to re-grade the site or add special drainage systems depending on the existing slope. For example, a flat grade tends to cause water to sit; a sloped grade tends to drain water better.
Concrete Foundations and Soil Conditions
Drainage, the movement of water downward through the soil, is typically rapid in sandy soils and slow in clay. A given amount of water can penetrate about three times deeper in sand than in clay, so it’s apparent that soil type will affect the drainage system you place around your concrete foundation.
A soil engineer is the best person to determine your soil conditions. Soil engineers possess a thorough knowledge of soil-structure interaction. They investigate areas proposed for development, analyze site and subsurface conditions, and make recommendations for septic systems, grading, earth support, drainage, foundation design, concrete slab on grade construction, and site remediation.
SPECIAL CONCRETE APPLICATIONS
There are many different kinds of concrete used in construction today. Each type blends a variety of materials to achieve unique characteristics. Structural concrete is used for building foundations and support beams. Insulating concrete is lightweight and can be used for finishes. Concrete can either be flat or shaped into three-dimensional objects. If you need steps, curbs, or other form work, please let your concrete contractor know ahead of time.
Concrete can also come in a wide variety of colors created by adding dyes to the liquid mixture. Fixing damage to colored concrete is tricky. Getting the right blend of colors is not an exact science. Don’t expect a repair person to create the perfect match. If a perfect match is critical, consider removing and replacing the area with new concrete lay.
CONCRETE SURFACES COME IN THREE DIFFERENT FINISHES:
Smooth Concrete Finish: The most common interior finish is really smooth, created by running a flat trowel over the top. This can be almost like glass.
Textured Concrete Finish: Smooth surfaces won’t work well outside, however. A little water can turn a smooth concrete surface into a slip hazard. Textured concrete is created to wick away water and provide traction for your outdoor concrete installations.
Exposed Aggregate Finish: Exposed aggregate is a rougher finish and less commonly used. Essentially, the gravel is embedded into the surface, creating an ultra-textured concrete. A construction expert can tell you which kind of concrete is best for your building needs.
Roof Installation or Repair
ABOUT ROOFING SHINGLES
There are two main types of roofing shingle: wood and asphalt. Western Red Cedar is a popular material for wood roofing shingles. The shingles may be Handsplit and Resawn, Tapersplit, Straight-split, or Tapersawn. Hip and Ridge Units are also available. The term Shakes is used to describe more rustic, rough-hewn shingles. Roofing Shingles and Shakes come in varying lengths, usually 16, 18 or 24 inches, and in random widths. Asphalt roofing shingles are available in three main forms: organic asphalt shingles, laminated organic asphalt shingles, and fiberglass asphalt roofing shingles.
CHOOSING THE BEST TYPE
Asphalt shingles
Your main choices are construction and style. As to construction, the cheapest asphalt shingles are made from paper (ususally recycled) which is soaked in asphalt to make it waterproof. A top surface of adhesive asphalt is added, with ceramic granules embedded to give further protection from the weather. More expensive shingles have a base mat of glass reinforced fiber, to which the asphalt is applied. This produces a much longer lasting shingle. Durability is reflected in the warranty period which can range from ten years up to fifty years in the case of high quality fiberglass-based shingles.As to style, some shingles are designed to resemble slate, others are designed to resemble traditional wooden shingles. In the case of the slate-look shingles, there are several options in terms of edge shape – these may be straight, rounded, octagonal, or irregular. There are also color choices including grey, black, brown, and green. In the case of wood-look shingles there is a choice from the cheapest regular designs to more expensive irregular designs which more closely resemble real wood shingles. There is also a color choice ranging from light to dark brown.
WOOD SHINGLES
The most common type of wood for wood shingles, also known as roofing shakes, is Western Red Cedar, which weathers to an attractive silvery grey. The main choices for wood roofing shingles are their size, and the option of split or sawn surface. The choice of size typically includes 16″, 18″ and 24″ length. All are perfectly practical, and the choice really comes down to aesthetics. Sawn shingles have a smooth surface on both sides. Split and re-sawn wood shingles are initially split, rather than sawn. The split shingle is then sawn to give one smooth side and one textured side. This type of roofing shingle is more expensive than the simple sawn version, but gives a very traditional rustic look – ideal for country properties.
Have a project in mind?
We do Residential, Commercial & Industrial Properties
Licensed as Ontario Corporation. Fully Insured & Bonded for your project.
Receive a $500 gift from us!
Whether it’s a small project or a bigger renovation, Ottawa Home Renovation’s team can help! With over 20 years of experience, we can help you make the most out of your home.
Already have a project in mind? Take advantage of our $500 rebate!
*Spend $2,000 or more on a home renovation, bathroom renovation, kitchen renovation or landscape project. Some conditions may apply.